Services
Glass Science
Glass: a hard substance, usually quite-brittle and transparent, composed chiefly of silicates and an alkali, fused at very high temperature. Often called a 'supercooled liquid,' because of its physical properties, which behave similarly to viscous media.
Composition and Properties of Glass
Most glass is a mixture of silica obtained from beds of fine sand or from pulverized sandstone; an alkali to lower the melting point, usually a form of soda or, for finer glass, potash; an alkaline-earth, such as lime as a stabilizer; and cullet (waste glass) to assist in melting the mixture. The properties of glass are varied by adding other substances, commonly in the form of oxides, [e.g., lead, for brilliance and weight; boron, for thermal and electrical resistance; barium, to increase the refractive index, as in optical glass; cerium, to absorb ultraviolet rays; transition-metal oxides, to impart color; and manganese oxide, for decolorizing.] The term “glass crystal,” derived from rock-crystal, is actually a misnomer and was first applied to clear, highly refractive glass. In the trade, it has come to denote a high-grade, colorless glass (Flint glass) and is sometimes applied to any fine hand-blown glass.
The Process of Glassmaking
The processes of glassmaking have remained essentially the same since ancient times. The materials are fused at high temperatures in ceramic containers, outgassed, skimmed, and cooled several hundred degree. At this point, the molten glass is ladled or poured into molds and pressed, or is blown (sometimes into molds), or is drawn. The shaped glass is annealed to relieve stresses caused by uneven cooling, and, then is slowly cooled. The glass, may be annealed on shelves, in an annealing oven, or carried on rollers, through annealing ovens, called lehrs.
Although, today, most hollow vessels, such as light bulbs or containers are machine blown, fine ornamental hollow ware is still made by gathering a mass of glass at the end of a long, iron blowpipe, blowing it into a pear-shaped bulb. This bulb is rolled on an oiled slab (marver), shaped with tools, and then reblown, often into a mold. The glass is reheated periodically in a small furnace (glory hole). Eventually, it is transferred to an iron rod (punty) attached to the base of the vessel, and the lip is shaped and smoothed. Methods of decoration include cutting, copper-wheel engraving, etching with hydrofluoric acid, enameling, gilding, and painting.
Development of the Glass Industry
Humans have used glass since prehistoric times, at first fashioning small objects from natural glass such as obsidian, a volcanic glass, or from rock crystal, a colorless, transparent quartz whose brilliance and clarity are emulated in manufactured glass. Glass is one of the most ancient of all materials known and used by mankind. The geologic glass, obsidian was first used by man thousands of years ago to form knives, arrow tips, jewelry etc.
Ancient Glassmaking
The place and date of origin of manmade glasses are not known. Manmade glass objects appear to be first reported in the Mesopotamian region as early as 4,500 BC. Glass objects dating as old as 3,000 B.C. have also been found in Egypt, where the industry was well established. The Egyptians had an alkali-lime-silicate composition, which rivals the best commercial compositions available today. Many varieties of glass were known during Roman times (circa 1500 B.C.), including cameo glass, such as the Portland vase, and millefiore glass, produced from fused and molded bundles of thin glass rods of many colors. Glass was also used for window panes, mirrors, prisms, and magnifying glasses. Except for the work done in Constantinople, little is now known of the methods of glassmaking used in Europe from the fall of Rome until the 10th cent., when stained glass came into use.
Early European Glassmaking
Venice was the leader in making fine glassware for almost four centuries after the Crusades and attempted to monopolize the industry by strict control at Murano of glassworkers, who were severely penalized for betraying the secrets of the art. After the invention (c.1688) of a process for casting glass, France was for many years supreme in the manufacture of plate glass such as that used to line the Galerie des Glaces at Versailles. Late in the 17th cent. England began to make flint glass, whose lead oxide content imparted a brilliance and softness that made it suitable for cut glass.
Glassmaking in Colonial America
The first glass factory in America was built in 1608, and glass was carried in the first cargo exported to England. Although other glasshouses were operated in the colonies, especially in New Amsterdam, the first successful and enduring large-scale glasshouse was set up by the German-born manufacturer Caspar Wistar in New Jersey in 1739. Some of the finest colonial glassware was produced in the Pennsylvania glasshouses of the German-born manufacturer H. W. Stiegel.
Beginnings of the Modern Era
The invention of a glass-pressing machine (c.1827), used by the American manufacturer Deming Jarves in his Boston and Sandwich Glass Company (1825–88), permitted the manufacturing of inexpensive and mass-produced glass articles. Nevertheless, in the 19th and 20th cent., there remained a sense of pride in individual craftsmanship. The American artist Louis C. Tiffany was responsible for the design and manufacture of an extraordinary iridescent glass used in a variety of objects in the late 1800s. Exceptionally fine blown glassware has been designed by such artists as René Lalique and Maurice Marinot in France, Edvard Hald and Simon Gate in Sweden, as well as Sidney Waugh in the United States.
Natural Glass
Although glass is a manufactured material, there exist several forms of naturally formed glass. When lightning strikes a mass of sand containing the right combination of minerals, objects called fulgurites are formed. Brittle, glassy tubes, fulgurites preserve the shape of the lightning strike as it diffuses through the sand. Tektites, smooth, dumbbell-shaped glassy objects, are the result of molten blobs of rock thrown up into the air when a meteorite hits the earth. Volcanic glass, or obsidian, is formed when the intense heat of a volcano fuses sand. Hard, black, and shiny, obsidian forms sharp edges when broken and can be easily worked to make bowls, mirrors, jewelry, knives, arrows, and spearheads. The Native peoples of western Canada traded obsidian from the Yukon and Alaska up and down the Pacific coast.
Contemporary Applications of Glass
Glass has become invaluable in modern architecture, illumination, electrical transmission, instruments for scientific research, optical instruments, household utensils, and even fabrics. New forms of glass, new applications, and new methods of production have revolutionized the industry. Recently developed forms of glass include safety glass, which is usually constructed of two pieces of plate glass bonded together with a plastic that prevents the glass from scattering when broken; fiberglass, which is made from molten glass formed into continuous filaments and used for fabrics or for electrical insulation; and foam glass, which is made by trapping gas bubbles in glass to yield a spongy material for insulating purposes. Certain uses of glass are now being superseded by newly developed plastics.
There are a host of glasses made for various optical and electro-optical purposes, which are based on unusual mixtures of rare earth oxides, zinc oxide and heavy metal oxides. These glasses normally have very little silica; instead using either Boron oxide or Phosphorous oxide as their predominant 'glass former.' These glasses find applications in Night Vision Technology, Metrology, Mass Spectrometry and Space Telescopy.
Exotic glasses can be made by combining the elements of semiconductors and chalcogens; such as Arsenic, Antimony, Tellurium, Selenium, Germanium and Sulphur. These 'Chalcogenide' glasses are used to transmit infrared energy and permit the manufacture of optics for night vision, FLIR's and infrared thermographic instrumentation.
Infrared Themography
Introduction
Infrared thermography is an excellent condition monitoring tool to assist in the reduction of maintenance costs on mechanical equipment. The technique allows monitoring of temperatures and thermal patterns, while equipment is online and running under full load. Most mechanical equipment has allowable operating temperature limits that can be used as guidelines.
Unlike many other test methods, infrared can be used on a wide variety of equipment, including: pumps, motors, bearings, pulleys, fans, drives, conveyors etc. This section will explain the benefits of Infrared Thermography, as a condition monitoring tool for plant mechanical systems.
We will highlight a few uses of infrared thermography as applied to analysis of mechanical equipment.
Infrared thermography is an electronic technique that allows us to see thermal energy. With this new capability plant maintenance personnel have recognized infrared thermography as one of the most versatile and effective condition monitoring tools available, today. Thermal imaging enhances a company's ability to predict equipment failure and plan corrective action, before a costly shutdown, equipment damage, or personal injury occurs.
Hi Temperature Clean Room Oven
FEATURES:
-
Digital Temperature Control (advanced PID) from Room Temperature to 425oC
- Single Ramp // Setpoint Version // Dual Display with Setpoint/Actual
- 8-Segment Ramp // Setpoint Version// Dual Display with Setpoint/Actual
- Solid State Relay Output, Controller Accuracy: ±0.5oC at all temperatures.
- Polished Stainless Steel Interior: 18 x 18 x 18 inches with adjustable height shelving.
- Dual Vents with User Enabled, low noise, Electric Fan.
- Insulation: Special CES high temperature insulation pack and clean room seal system.
- Power: 1500 Watts, 120 VAC, 13.8 Amps, 50/60 Hz for benchtop use. (14 gauge cable with Grounded Plug).
- Overall Dimensions: 24 x 24 x 32 inches high.
- Weight: 115 pounds (52 Kg).
General Installation Information:
- Mount on a fireproof or fire-retardant table top, at 30 to 36 inches from floor level.
- Connect to a dedicated 15 amp circuit breaker.
- Provide a minimum of 12-inches clearance on all sides.
Reactive Gas Ovens
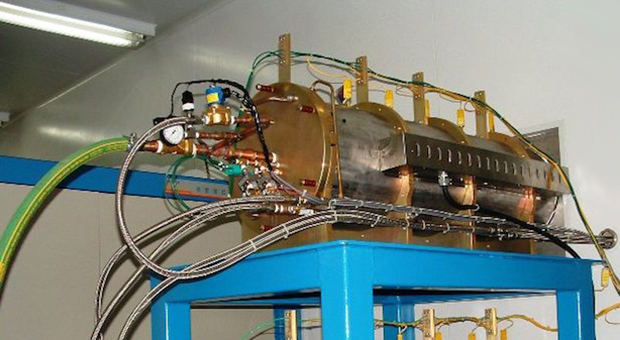
BASIC FEATURES:
-
Digital Temperature Control (advanced PID) from Room Temperature to 1150oC
- Single Ramp // Setpoint Version // Dual Display with Setpoint/Actual
- 8-Segment Ramp // Setpoint Version// Dual Display with Setpoint/Actual
- Solid State Relay Output, Controller Accuracy: ±0.75oC at all temperatures.
- Temp Profile: Adjustable, based on T/C placement and water cooling.
-
Stainless Steel or Inconel Retort (optional): Ø5-inch or Ø6-inch pipe x 72 to 84 inches total length, with removable shelving.
- Water Cooled: Low flow rate (<4 LPM inlet @ RT ) with water flow safety switch.
- CES proprietary-design, Bulkhead Doors with side-mounted gas ports.
- 1-NPT Exhaust porting
- Vacuum Capable (option): Pressures to less than 1 micron.
- 1, 2 or 3 Gas Mass Flow Controllers with manual and/or pc control, digital setpoints (full scale ranges from 0-1 thru 0-10 SLPM).
- Insulation: Special CES high temperature, hig efficiency insulation pack and clean room seal system.
- Typical Power: 11,500 Watts, 240 VAC, 48 Amps, 50/60 Hz , 1Ø for benchtop use. (three-3 phase Ø and other power versions available).
- Overall Dimensions: 24W x 27H x 80 inches Long.
- Weight: approx 315 pounds (143 Kg). with Ø6 x Sch-40 pipe.
- Computer Interface (optional): Controls all temperature functions, controls all gas valves and mass flow controllers, monitors all safety features and performs datalogging, using simple to learn CES software packages.
General Installation Information:
- Mount on a fireproof or fire-retardant table top, at 30 to 36 inches from floor level.
- Connect to a dedicated 60 amp circuit breaker.
- Provide a minimum of 12-inches clearance on all sides.
CPS Inert Gas Processing Furnace
Coming soon...